SS Reactor
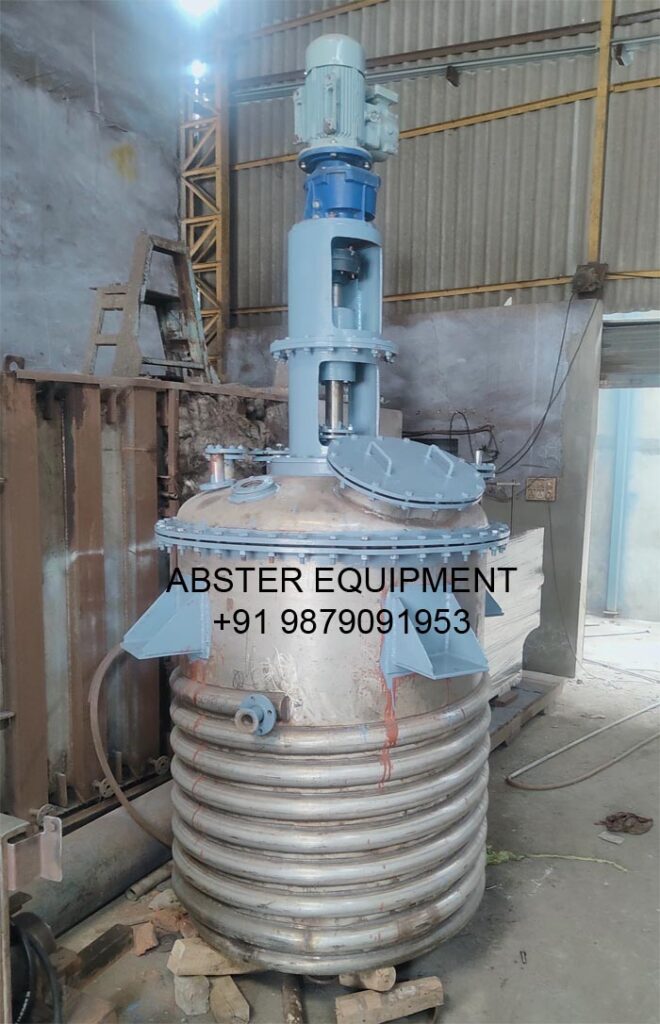
Description
A stainless steel (SS) reactor is a vessel made of high-quality stainless steel that’s used in various industries to create a controlled environment for chemical reactions: chemical, pharmaceutical, food, and biotechnology.
SS reactors are designed to withstand harsh conditions, corrosive materials, and extreme temperatures. They’re also durable, easy to clean, and have high temperature resistance and corrosion resistance. Some examples of SS reactors include:
500C High Temperature Limpet Reactor: Has a storage capacity of 500 L and a maximum temperature of 500°C
Stainless Steel Chemical Reactor: Has a capacity of 1000 L and a maximum design pressure of 10 bar
SS 306 Stainless Steel Fermenter: Has a gas yield of 30 m^3/day
SS reactors typically include the following components:
Inner tank
Outer tank
Heating and cooling systems
Agitators
Control systems
Double jacket for heating and cooling to control the process heat inside the reactor
Some examples of SS reactors include:
500C High Temperature Limpet Reactor: Has a storage capacity of 500 L and a maximum temperature of 500°C
Stainless Steel Chemical Reactor: Has a capacity of 1000 L and a maximum design pressure of 10 bar
SS 306 Stainless Steel Fermenter: Has a gas yield of 30 m^3/day
Limpet Coil SS Reactor
MS jacketed Reactor
Industrial Reactor
We are a leading Manufacturer of chemical process reactor, ms jacketed reactor, industrial chemical reactor, hydrogenation industrial reactor, resin plant reactor and stainless steel chemical reactor from Mumbai, India.
Stainless steel reactors are specialized vessels used for conducting chemical reactions, mixing, blending, and processing various materials. They are constructed from high-quality stainless steel alloys, which offer superior corrosion resistance, durability, and strength. These reactors are designed to operate under controlled conditions, such as specific temperatures, pressures, and agitation rates, to ensure consistent and efficient processing.
Types of Stainless Steel Reactors
Stainless steel reactors come in various types to cater to different industrial needs and applications. The most common types include:
1. Jacketed Reactors
Jacketed reactors feature an outer jacket surrounding the reactor vessel, allowing for efficient heat transfer. This design enables precise temperature control by circulating heating or cooling media through the jacket. Jacketed reactors are widely used in processes that require precise temperature regulation, such as chemical synthesis, polymerization, and distillation.
2. Pressure Reactors
Pressure reactors are designed to withstand high pressures, making them suitable for reactions that require elevated pressure conditions. These reactors are equipped with robust sealing mechanisms and reinforced walls to ensure safe operation under high-pressure environments. Pressure reactors are commonly used in hydrogenation, polymerization, and supercritical fluid extraction processes.
3. Agitated Reactors
Agitated reactors feature an impeller or agitator system that promotes efficient mixing and dispersion of reactants. These reactors are essential for processes that require homogeneous blending, such as emulsification, suspension polymerization, and fermentation. Agitated reactors can be further classified based on the type of agitator used, such as anchor, turbine, or helical impeller.
4. Batch Reactors
Batch reactors are designed for processing materials in discrete batches. These reactors are commonly used in the pharmaceutical, fine chemical, and specialty chemical industries, where precise control over reaction conditions and product quality is crucial. Batch reactors can be equipped with various features, such as heating/cooling jackets, agitation systems, and sampling ports, to facilitate efficient batch processing.
5. Continuous Reactors
Continuous reactors are designed for continuous processing, where reactants are continuously fed into the reactor, and products are continuously removed. These reactors are commonly used in large-scale chemical production processes, such as polymer synthesis, petrochemical processing, and bulk chemical manufacturing. Continuous reactors offer high throughput and consistent product quality.
Materials for Stainless Steel Reactors
The selection of the appropriate stainless steel alloy is crucial for ensuring the reactor’s performance, durability, and compatibility with the processed materials. The most commonly used stainless steel grades for reactor construction include:
1. Austenitic Stainless Steels
Austenitic stainless steels are widely used in reactor construction due to their excellent corrosion resistance and high strength at elevated temperatures. These alloys contain chromium, nickel, and sometimes molybdenum, which enhance their resistance to various corrosive environments.
2. Duplex Stainless Steels
Duplex stainless steels, such as 2205 and 2507, offer a combination of high strength and superior corrosion resistance. These alloys contain a balanced mixture of austenite and ferrite phases, making them suitable for applications involving highly corrosive environments and high mechanical stress.
3. Super Austenitic Stainless Steel
Super austenitic stainless steels are designed for exceptional resistance to pitting, crevice corrosion, and stress corrosion cracking. These alloys contain higher levels of chromium, nickel, and molybdenum, making them suitable for highly aggressive environments and high-temperature applications.
4. Nickel-Based Alloys
Nickel-based alloys, such as Hastelloy and Inconel, are used in reactors that require exceptional resistance to highly corrosive environments, high temperatures, and oxidizing conditions. These alloys are commonly used in the chemical processing, petrochemical, and nuclear industries.
Design Considerations for Stainless Steel Reactors
The design of stainless steel reactors is a critical aspect that ensures their safe and efficient operation. Several factors must be considered during the design process, including:
1. Reactor Geometry
The geometry of the reactor, including its shape (cylindrical, conical, or spherical), dimensions, and volume, is determined based on the specific process requirements, such as the desired reaction kinetics, heat transfer, and mixing efficiency.
2. Pressure and Temperature Ratings
Stainless steel reactors must be designed to withstand the anticipated operating pressures and temperatures. Factors such as the reactor material, wall thickness, and reinforcement structures are carefully considered to ensure safe operation under extreme conditions.
3. Agitation and Mixing Systems
For processes that require efficient mixing or agitation, the reactor design must incorporate appropriate agitation systems, such as impellers, baffles, or static mixers. The selection and placement of these components are crucial for achieving the desired mixing performance.
4. Heating and Cooling Systems
Depending on the process requirements, stainless steel reactors may be equipped with heating or cooling systems, such as jackets, coils, or external heat exchangers. These systems ensure precise temperature control and efficient heat transfer during the reaction or processing steps.
5. Instrumentation and Control Systems
Modern stainless steel reactors are often integrated with advanced instrumentation and control systems to monitor and regulate various process parameters, such as temperature, pressure, pH, and flow rates. These systems enable precise process control and data acquisition for quality assurance and process optimization.
6. Safety Features
Safety is a paramount consideration in the design of stainless steel reactors. Features such as pressure relief valves, rupture discs, emergency venting systems, and containment structures are incorporated to mitigate potential hazards and ensure the safe operation of the reactor.
Applications of Stainless Steel Reactors
Stainless steel reactors find applications across a wide range of industries due to their versatility, durability, and compatibility with various materials and processes. Some of the key applications include:
1. Chemical Industry
Stainless steel reactors are extensively used in the chemical industry for various processes, such as chemical synthesis, polymerization, hydrogenation, oxidation, and catalytic reactions. They are employed in the production of bulk chemicals, fine chemicals, specialty chemicals, and intermediates.
2. Pharmaceutical and Biotechnology
The pharmaceutical and biotechnology industries rely heavily on stainless steel reactors for the synthesis of active pharmaceutical ingredients (APIs), biopharmaceuticals, and other drug products. These reactors ensure product purity, sterility, and compliance with stringent regulatory requirements.
3. Food and Beverage Processing
Stainless steel reactors are widely used in the food and beverage industry for processes such as fermentation, pasteurization, and the production of food additives, flavors, and ingredients. Their corrosion resistance and ease of cleaning make them ideal for maintaining food safety and quality standards.
4. Petrochemical and Refining
The petrochemical and refining industries utilize stainless steel reactors for various processes, including hydrocracking, hydrotreating, and catalytic reforming. These reactors are designed to withstand the harsh conditions encountered in these industries, such as high temperatures, pressures, and corrosive environments.
5. Environmental and Waste Treatment
Stainless steel reactors play a crucial role in environmental and waste treatment applications, such as water treatment, wastewater treatment, and hazardous waste processing. Their corrosion resistance and durability ensure the safe and efficient handling of various contaminants and pollutants.
6. Renewable Energy and Biofuels
The production of biofuels and renewable energy sources often involves chemical processes that require stainless steel reactors. These reactors are used for processes such as biomass conversion, fermentation, and catalytic upgrading of bio-based feedstocks.
Maintenance and Upkeep of Stainless Steel Reactors
Proper maintenance and upkeep are essential for ensuring the longevity and optimal performance of stainless steel reactors. Here are some key considerations:
1. Cleaning and Passivation
Regular cleaning and passivation of stainless steel reactors are crucial to maintain their corrosion resistance and prevent contamination. Cleaning procedures may involve chemical cleaning agents, mechanical cleaning methods, or a combination of both, depending on the specific application and contaminants.
2. Inspection and Testing
Periodic inspections and testing of stainless steel reactors are necessary to detect any signs of wear, corrosion, or damage. Non-destructive testing methods, such as visual inspection, ultrasonic testing, and dye penetrant testing, can be employed to assess the reactor’s condition and identify potential issues.
3. Gasket and Seal Replacement
Gaskets and seals are critical components that ensure the integrity of stainless steel reactors. Regular replacement of these components is recommended to prevent leaks and maintain the reactor’s pressure and temperature ratings.
4. Agitator and Impeller Maintenance
For agitated reactors, regular maintenance of the agitator system, including impellers, shafts, and bearings, is essential to ensure efficient mixing and prevent premature wear or failure.
5. Calibration and Validation
Instrumentation and control systems associated with stainless steel reactors require regular calibration and validation to ensure accurate and reliable process monitoring and control.
6. Training and Safety Protocols
Proper training of personnel involved in the operation and maintenance of stainless steel reactors is crucial for ensuring safe and efficient operations. Adherence to safety protocols, such as lockout/tagout procedures, personal protective equipment (PPE) requirements, and emergency response plans, is essential to mitigate potential risks.
S S reactors are versatile and robust equipment that play a vital role in various industries. By understanding their types, materials, design considerations, applications, and maintenance requirements, manufacturers and operators can optimize their processes, ensure product quality, and maintain a safe and efficient working environment.